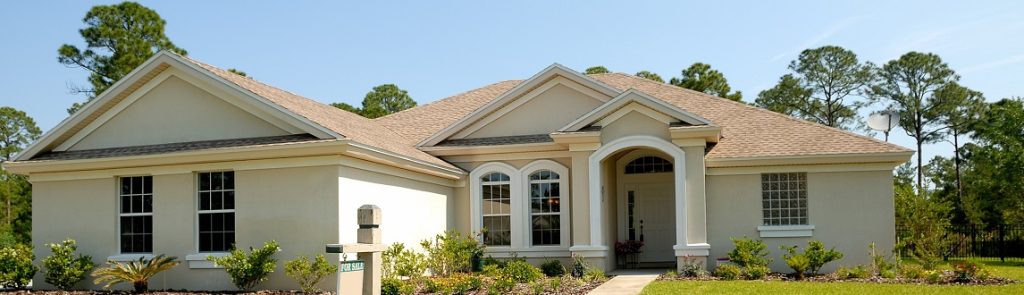
As the Supply Chain Saga Continues…
We’re a few weeks into 2022 now. Building materials are still backed up in supply chains. For many home developers, building projects have lagged.
Pauses in processing, followed by delayed production schedules, were among the immediate effects of the pandemic. In 2021, the vast majority of building companies struggled with supply delays. Even though analysts have predicted that the clogs will start to clear in mid-2022, the demand has been building up for a long time.
It’s a hurry-up-and-wait situation for construction firms. Out-of-stock selections can mean having buyers move in before houses are finished. A widely noted piece on new owners having to move into unfinished homes appeared in The Wall Street Journal in January 2022.
High Demand, Low Supplies
Windows, paint, nuts and bolts, screws and washers, garage doors, washing machines, and anything with electronic controls (given the acute semiconductor shortages) are all beset by backups. On account of high prices for hard-to-find supplies, some building projects are on hold indefinitely. If, for example, windows won’t be in stock for four months, construction timelines could be paused for six months.
An Ohio developer, Epcon Communities, has asked home buyers to move in now and wait for their gutters to be attached later. Builders in Sacramento, California recently got the city’s go-ahead to give buyers the keys before permanent garage doors are in place.
Some warehouses are holding large inventories of materials, trying to anticipate their needs in advance. That puts them at risk of paying steep prices for products that could later drop in price. It also adds confusion to the picture. It’s hard to tell which products are in the throes of severe shortages, and which are largely being warehoused. But some backups are confirmed and have become entrenched. Take chip manufacturing for semiconductors. The Commerce Department indicates that the shortage will continue to stall the electronics sector for most of 2022.
Where Is the Wood?
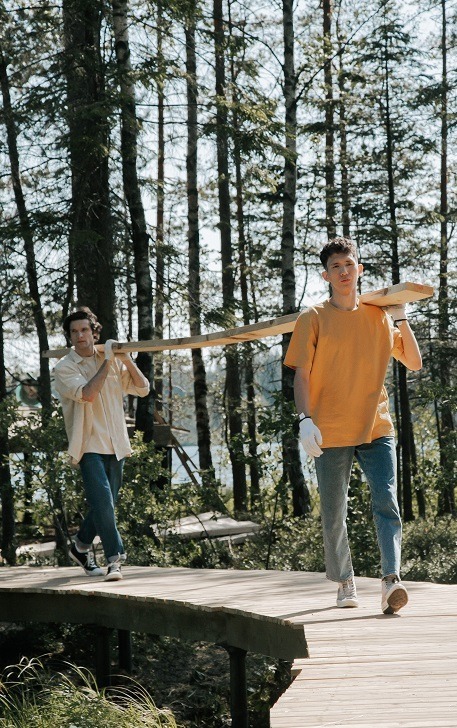
Lumber prices are being carefully watched in the industry. They topped $1500 per 1,000 board feet as the pandemic — and economic fear — understandably spread. Then the people working from home started a flurry of DIY projects. Demand rose. Production rose in turn, and caught up with demand. Lumber prices drifted down in mid-2021 to $500 and below.
But by late 2021, scarcity again took over. What happened? The United States hiked tariffs on lumber from Canada, while wildfires took their toll on the western woods. Lumber prices ultimately surged to $1,200.
The omicron variant has exacerbated this new wave of backups and price hikes. Worker illnesses have closed factories, slowed shipments, and left docks to fill up with unloaded cargo. This comes on top of underlying problem of international proportions: “an overstretched skilled workforce” which has kept companies all over the world from taking on new projects.
A Domino Effect
As key materials become increasing elusive, builders scramble for more plentiful alternatives. This has had the effect of increasing prices for anything that’s used. Metal products for builders have risen in price by more than 40 percent and plastic construction materials are up more than 30 percent. Steel mill products in general have more than doubled. And the year-over-year increase for asphalt is +83%.
The result? Buyers are paying very high prices for new construction since the pandemic began. The National Association of Home Builders says the price of a newly built home is up by more than $18,600.
But progress is happening. Wholesalers reported inventories were up about 2 percent in December 2021, after rising 1.7% in November.
Inventory accumulation had been constrained by COVID-19-related global shortages, and the solid increases over the last two months offer hope that the worst of the supply chain disruptions was behind.
The Fixer-Upper: Moving In Before It’s Finished
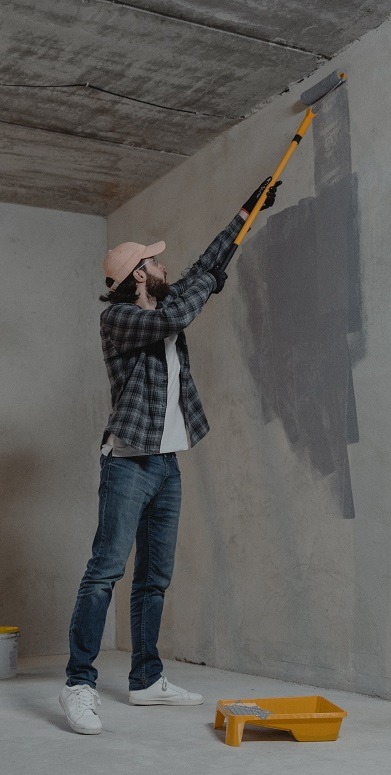
Some homeowners are in the middle of DIY upgrades, or have purchased an older home to renovate before moving in. Renting and rehabbing could be the best strategy for buying a house in super-competitive areas.
But DIY is becoming surprisingly costly, for reasons our readers now know. Given the price volatility for certain materials and fixtures, homeowners can easily spend all the money they’ve budgeted only to find out that they need more materials, or that key supplies simply aren’t available.
Is the home safe, well covered, and warm? Does it have at least one operable toilet and shower? Does its new owner have electricity and running water — and, better yet, finished floors? Then it could be possible, depending on local ordinances, to stop spending extra money on a temporary rental home. The owner may be able to move into the house, and sweep the rent funds into the renovation project.
☛ Bought a fixer-upper to turn into your dream home? A building permit could be necessary, to cover both outdoor and interior upgrades. Here’s Everything You Wanted to Know (or Not) About Permits.
One way to pull this off is to separate off one area of living space from the renovation work. Store personal effects off-site. Set up temporary bathroom fixtures. Permanent kitchen appliances can be purchased and can be moved over the floor as needed. After all the basic work is done, the owner can move everything in.
An owner can look into a personal loan to complete the work. It’s important to check the interest rates. Depending on a borrower’s credit profile, average interest runs anywhere from 10 to 30 percent.
Alternatively, buying a used mobile home could save the project. It’s one way to ensure the owner has a place to live on or near the property. After the project is done, the mobile home could be resold.
The Takeaway
Everyone’s been impressed with the quick recovery and continued rise of U.S. real estate. Yet the home building sector is simply not working to capacity at this time. This, although the demand for housing is practically off the charts, with several million fewer homes available than are needed.
There is no quick fix. Hopeful home buyers may feel like they’re enduring an incessant stream of challenges. If you’re among the hopefuls, at least you know you’re not alone.
Supporting References
Nicole Friedman for The Wall Street Journal: “Supply-Chain Issues Leave New Homes Without Garage Doors and Gutters,” (Jan. 9, 2022). Subscription required; material also available under the title “Supply Woes Leave New Homes Unfinished” (Jan. 11, 2022) through REALTOR.com®.
Iain Smith for Levelset.com: Homes Left Unfinished as Contractors Are Squeezed by Material Shortages (Jan. 14, 2022; citing the Producer Price Index: PPI Detailed Report from the U.S. Bureau of Labor Statistics, Nov. 2021).
Sara Savat-Wustl for Futurity.org: How Long Will the Supply Chain Crunch Last? (Nov. 17, 2021).
Trading Economics Data: Lumber.
National Association of Home Builders: Latest Wave of Rising Lumber Prices Adds More than $18,600 to the Price of a New Home (Jan. 4, 2022).
Medora Lee for The Balance: Lumber Prices Jump (Again), Increasing New Home Costs Off the Charts (Jan. 21, 2022).
Lucia Mutikani for Reuters: U.S. Goods Trade Deficit Hits Record High; Inventories Rise Strongly (Jan. 26, 2022).
Freddie Mac: Housing Supply: A Growing Deficit (May 7, 2021).
U.S. Department of Commerce: Results From Semiconductor Supply Chain Request for Information (Jan. 25, 2022).
Propeller Aerobotics Blog: How to Adapt to the Skilled Labor Shortage in Construction (Aug. 19, 2021).
Photo credits: Ron Lach, Tima Miroshnichenko, and Pixabay, via Pexels.